Contenidos
Las paradas no son una opción
En la producción industrial, cada segundo de una máquina detenida equivale a problemas para el negocio, sin importar el sector. Estas son algunas de las consecuencias más comunes:
- Rendimiento reducido.
- Aumento de costos.
- Atraso en órdenes de producción.
- Problemas con clientes.
- Daño a la reputación de la empresa si sucede de forma recurrente.
La pregunta clave es: ¿cuánto cuesta realmente una parada para tu negocio? Dependiendo de la industria, podría ser desde miles hasta millones de dólares, y las pérdidas no hacen más que crecer con el tiempo debido a factores como el aumento de los costos energéticos, materiales y mano de obra detenida.
Mi recomendación: Actúa antes de que sea tarde
Hoy en día contamos con herramientas que permiten adelantarnos a las fallas y planificar acciones preventivas, reduciendo al mínimo el impacto de las paradas no programadas. Estas son algunas soluciones clave que recomiendo implementar.
Mantenimiento preventivo: Tu primera línea de defensa
Prevenir es siempre más rentable que reparar. Algunas prácticas básicas para empezar:
- Aplicar rutinas de mantenimiento del fabricante.
- Mantener un stock adecuado de insumos.
- Actualizar periódicamente las máquinas.
- Llevar un registro detallado del mantenimiento de cada equipo.
Pero no te detengas ahí. Para equipos y procesos críticos, es esencial agregar monitoreo en tiempo real y generación automática de datos.
Visibilidad total del proceso productivo
La información es poder. Sistemas avanzados pueden traducir datos en indicadores clave como:
- OEE (Overall Equipment Effectiveness).
- TVC (Tiempo, Velocidad y Calidad).
Estos indicadores te permiten identificar tendencias y actuar antes de que los problemas escalen. Además, los operadores también pueden intervenir rápidamente en caso de fallas menores.
Herramientas de monitoreo: Tu aliado estratégico
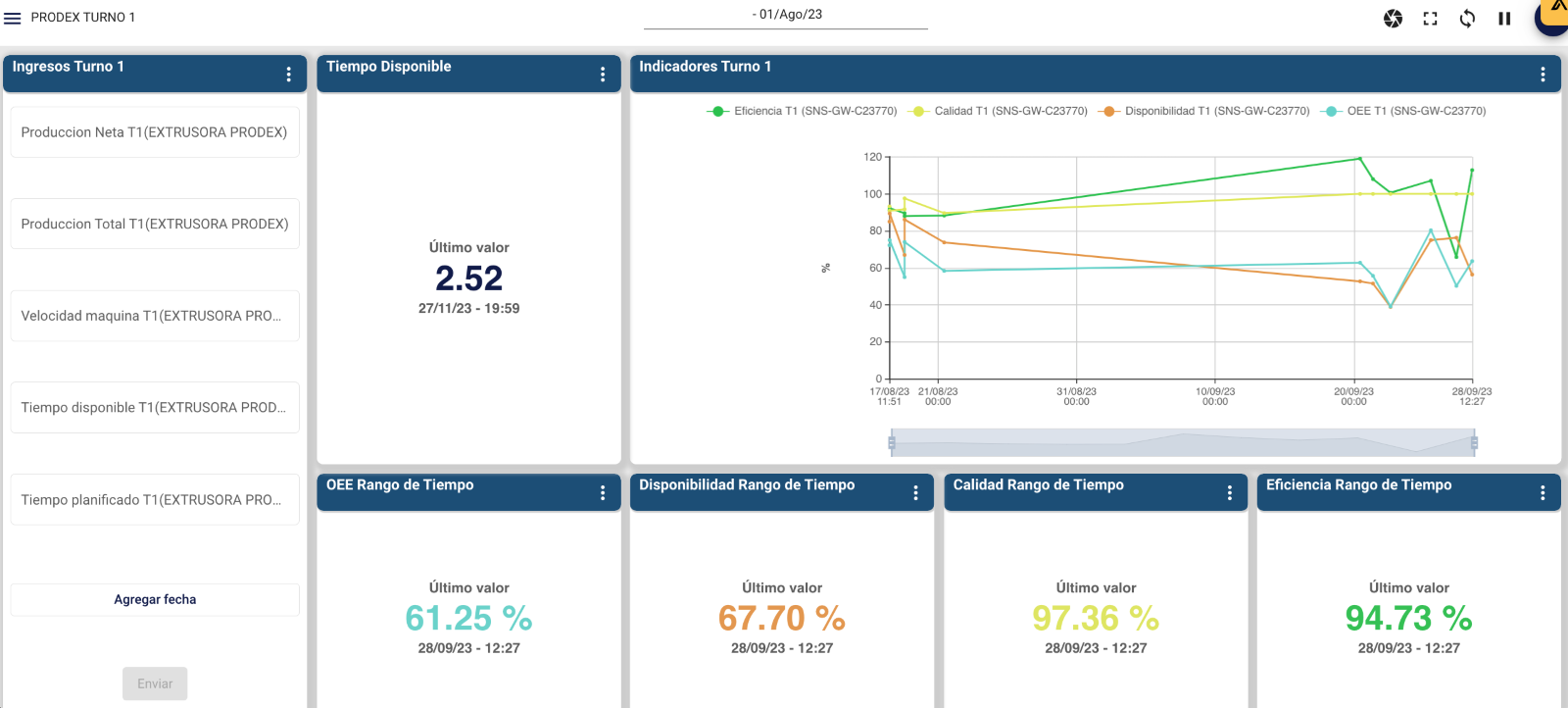
Imagen: Panel OEE en Sens Cloud
En la imagen que acompaña este artículo, se muestra un dashboard de monitoreo en tiempo real. Este tipo de herramienta ofrece:
- Producción neta y total: Una visión clara del rendimiento por turno.
- Velocidad de la máquina: Indicadores para medir la eficiencia operativa.
- Tiempos planificados y disponibles: Datos esenciales para prevenir interrupciones.
- Gráficos de tendencia: Ayudan a identificar patrones y prevenir problemas mayores.
Estas soluciones no solo transforman los datos en acciones, sino que también te dan un control total para tomar decisiones informadas.
Caso práctico: Sens Technologies y NextGen
Te doy un ejemplo concreto. Con hardware y software de Sens Technologies, de la línea Next Industrial-Tech de NextGen S.A., logramos extraer datos de controladores (PLC) y combinarlos con información ingresada por operadores. Esto permite generar indicadores como:
- Tiempo de uso productivo.
- OEE de la máquina.
- Disponibilidad, calidad y eficiencia.
Estos datos no solo optimizan el mantenimiento preventivo, sino que también ofrecen una visibilidad que ayuda a detectar mejoras o problemas con antelación.
Inteligencia Artificial: El futuro del mantenimiento
Si buscas adelantarte al futuro, integrar IA en tus procesos de mantenimiento es una inversión que vale la pena.
Mi consejo final
Si tienes dudas o quieres saber más sobre cómo implementar estas soluciones, estaré encantado de ayudarte. ¡Hablemos!